
Semi-passive and active TPS structures would include a working fluid and pumped coolant flow, respectively. The passive TPS have three structural types, namely, an insulated structure used for moderate heat fluxes for relatively short times, a heat sink structure used with a moderate heat flux for a transient situation, and a hot structure utilized for moderate heat flux for long periods of time. Three types of thermal management systems can be used to cool hypersonic or space reentry vehicles: passive, semi-passive, and active.
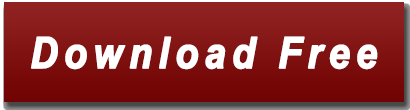
There are multiple options for dealing with the severe thermal environments encountered during hypersonic flight. TPS are required for a range of hypersonic vehicles ranging from ballistic reentry to hypersonic cruise vehicles, within both Earth’s atmosphere and non-Earth atmospheres. Aly-Hassan, in Multifunctionality of Polymer Composites, 2015 2.2.4.2 Semi-passive and active TPS challenges without working fluid or coolant flow The weight reduction potential for cooled CMC engine components is shown in Fig. Cooled CMCs are attractive for hypersonic engine components because of the following benefits: (1) lighter weight than metallic designs, with potential for 50% weight reduction (2) lower coolant flow requirements (3) potential elimination of reentry cooling requirements (4) allow for higher fuel injection temperatures and (5) increased operational margin that translates to enhanced range and/or system payload.
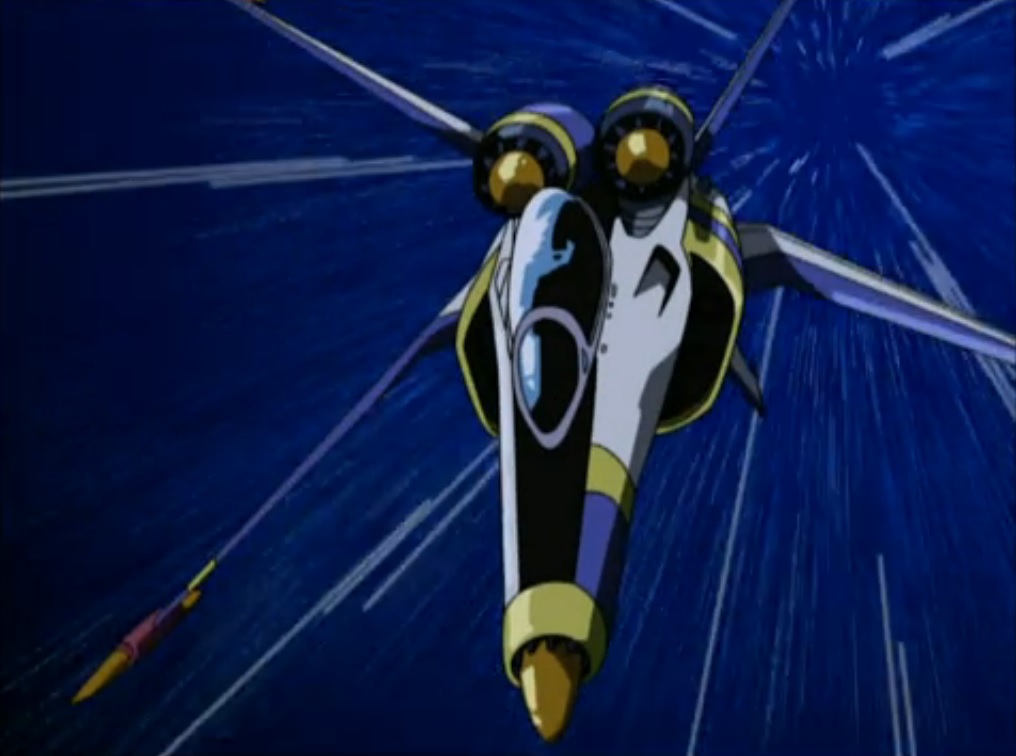
The current state-of-the-art materials for the various engine components are cooled high-temperature materials, including high-conductivity copper. Because of the temperature limitations of all material systems, cooling of engine components is required, as shown in Fig. 12.22. These extremely high temperatures pose significant material and structural challenges. The temperatures encountered in engine components (eg, inlet, combustor, and nozzle) are significantly higher than in the other structural components, as shown in Fig. 12.21.
